It almost feels like stepping into a time machine when I arrive at Bang & Olufsen’s factory in Struer, Denmark. A machine that goes forwards in time, but also backwards.
Because in addition to making visionary products in aluminium, the Danish manufacturer has a factory dedicated solely to the repair and restoration of old classics. There’s also a museum hall where you can see virtually every piece up close, including custom-painted versions of the flagship BeoLab 90, among others. And there, in a corner, is an old post-war wire recorder. And it works! “Tonmeister” Geoff Martin happily demonstrated with a home recording from around 1950 of a man talking and a woman playing the piano and singing. The sound is surprisingly clear for a recording made on a razor-thin wire!
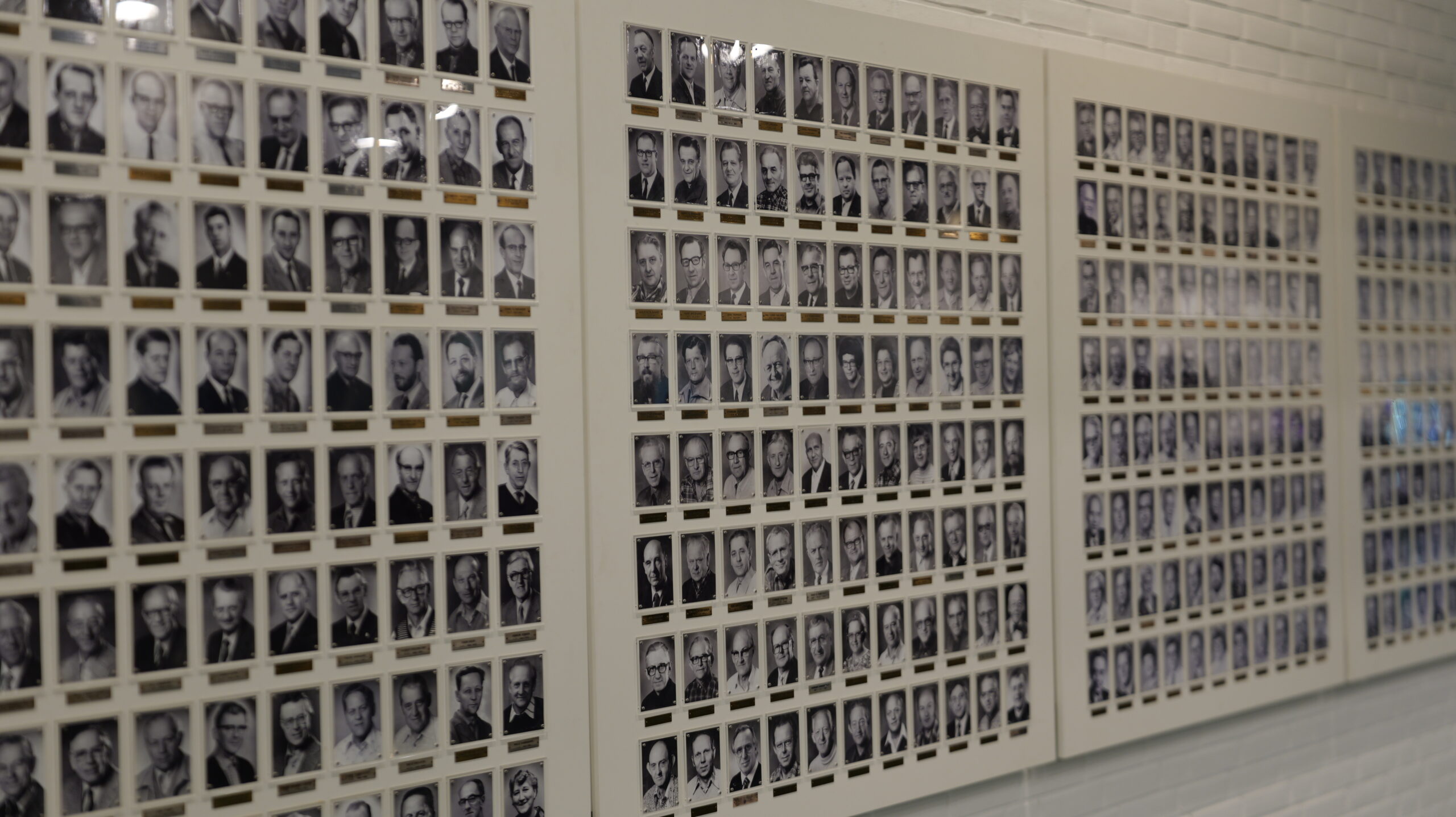
Over 500 employees
The factory in Struer is home to over 500 employees working with everything from design and acoustics to mechanics and software. In other words, it’s something of a cornerstone company in a small town of 10,000 inhabitants.
At the same time, history hangs heavy over the factory, which was bombed to smithereens by the Germans during the war. The founders had to roll up their sleeves and rebuild from scratch. Today, the proud heritage is evident in the walls, where veterans with up to 50 years of seniority perform daily routines that require both knowledge and patience.
Beolab 8 can be used as a standalone table speaker for pleasant background music or set up as a stereo set.
B&O has a seniority wall in the foyer – a Wall of Fame – where you get your picture hung on the day you’ve worked there for 25 years. There must be over a thousand pictures, with founder Peter Bang at the top left – followed by someone who happens to be called F. Olufsen. Co-founder Svend Olufsen is not on the wall, however, as he only managed to work there for 24 years before he tragically died during surgery. This means there are no exceptions from the rule…
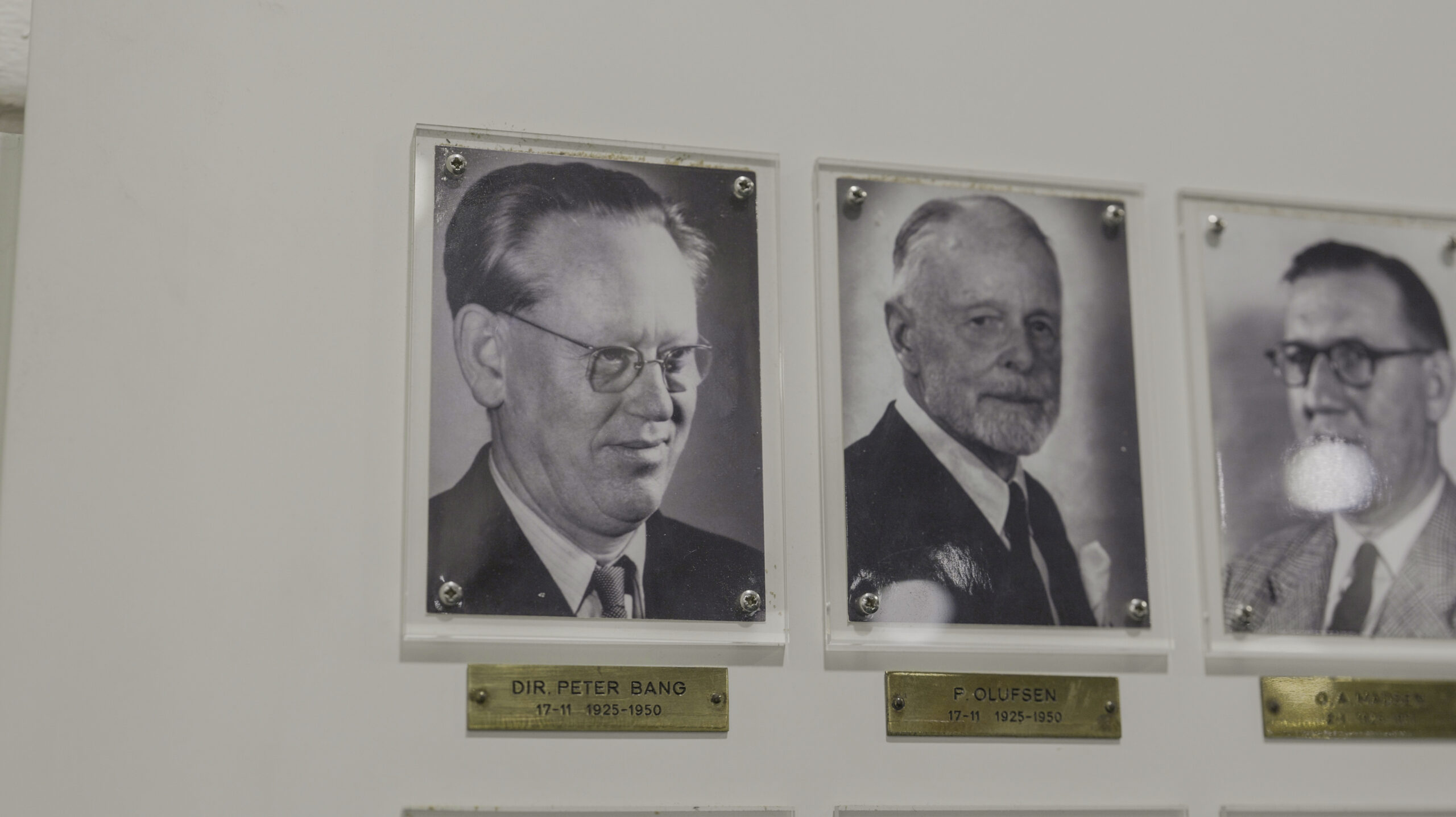
Factory 5: People, machines and lasers
After an introduction to the interesting history of the factory, we move on to the production facilities. Just inside the door of Factory 5, I’m greeted by a fascinating sight of robots and 3D printers doing precision work alongside experienced hands.
At one end, workers study aluminium parts under a magnifying glass to find the slightest scratch or risk of corrosion. At the other end, industrial robots mill shapes and frames out of aluminium pieces with surgical precision. The leftover chips are sold back to the supplier, minimising waste in production.
Beolab 8 can be used as a standalone table speaker for pleasant background music or set up as a stereo set.
Everywhere we look, activity is buzzing, and every now and then our paths are crossed by lorries carrying semi-finished products for milling, turning or polishing. Others transport finished products ready for quality control and packaging.
Every now and then I see the outlines of familiar Beolab speakers, from the unmistakable cone-shaped Beosound 2 to the brand new Beolab 8 and the monstrous Beolab 90. “No pictures, please” is unfortunately a common demand.
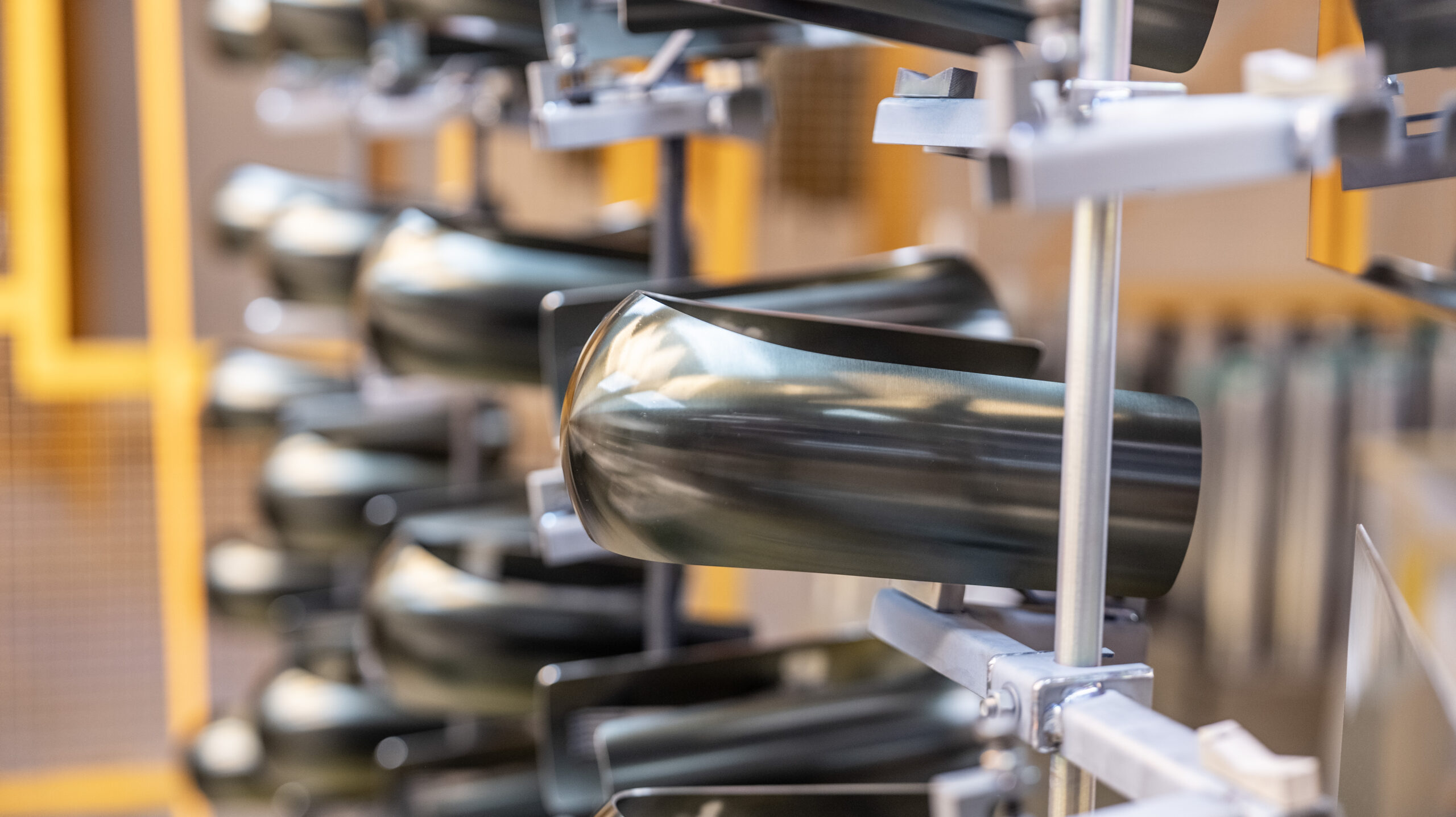
No quick shortcuts to quality
I’m struck by the care and vigilance that all processes require. Whether it’s aluminium sheets polished to a mirror-like finish, circuit boards soldered by hand, or lasers etching thousands of microscopic holes to create a backlit logo, the margins are microscopic.
Even the robots must first “learn” their movements from humans through an arduous process of detecting and decoding their actions. Then the robots can perform the same process and repeat it endlessly. And thus be able to perform insanely complex actions with a precision in each repetition that no human can master.
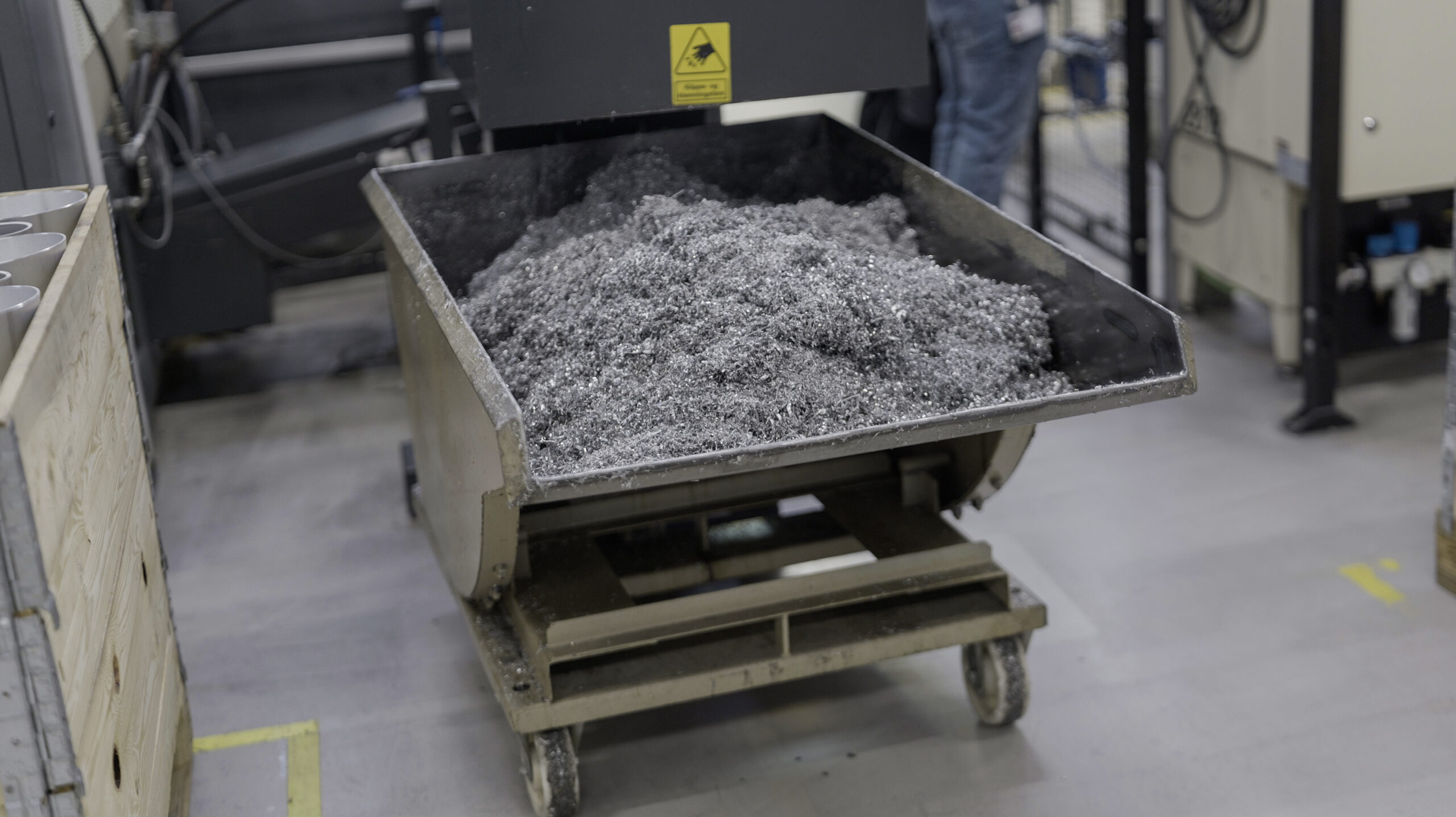
Bang & Olufsen costs more
This is clearly not a factory that cuts corners or prioritises quantity over quality. It’s that kind of meticulous precision work that strikes me: Of course these products cost more money! There’s no getting around that. You just don’t get this result with a cheaper process.
Beolab 8 can be used as a standalone table speaker for pleasant background music or set up as a stereo set.
I’ve spoken to people who automatically shout “scam and fraud” whenever something costs more than something else. I’m not blameless there either, and I’ve imagined that there are probably some smart types driving around in a Porsche or an Aston Martin. However, there were no such people to be seen in the large car park outside Bang & Olufsen’s premises. I was picked up from the airport in a small Volkswagen Up and escorted between factories in a Toyota Yaris. I know several public servants with a more extravagant lifestyle than the B&O people seem to practise…
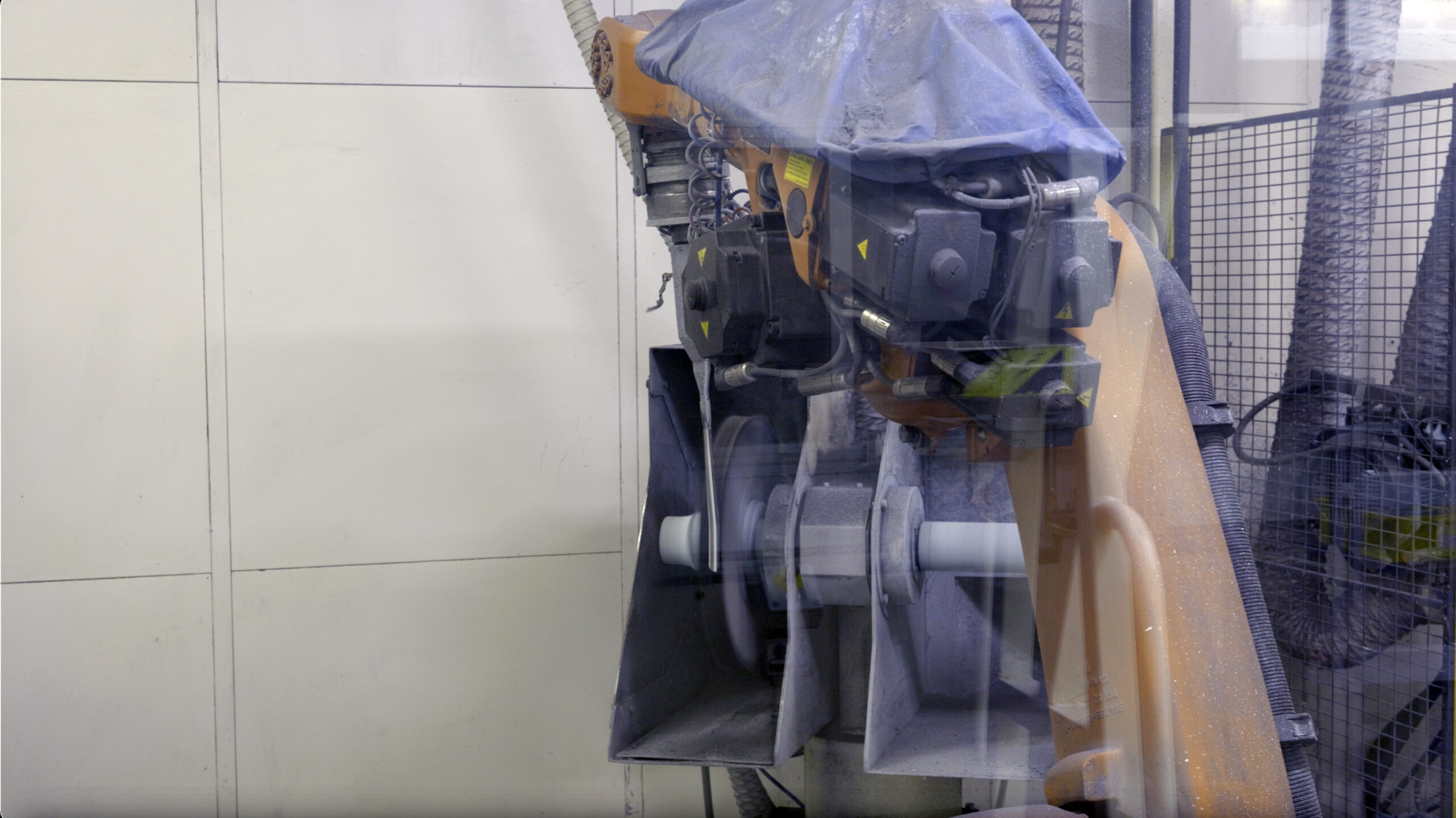
Factory 3: Caught up with the past
One place where history is strong is in the module service department at Factory 3, where they practice what may seem like a dying craft: repairing and restoring older Bang & Olufsen products.
Even modern appliances in need of a service pass through this area. But what really strikes me is the dedication to keeping vintage models like the Beogram turntables and Beocord cassette players alive.
Here, technicians sit with microscopes and soldering tools, pushing the boundaries to repair faulty circuit boards and components. B&O reports a success rate of an incredible 97 per cent!
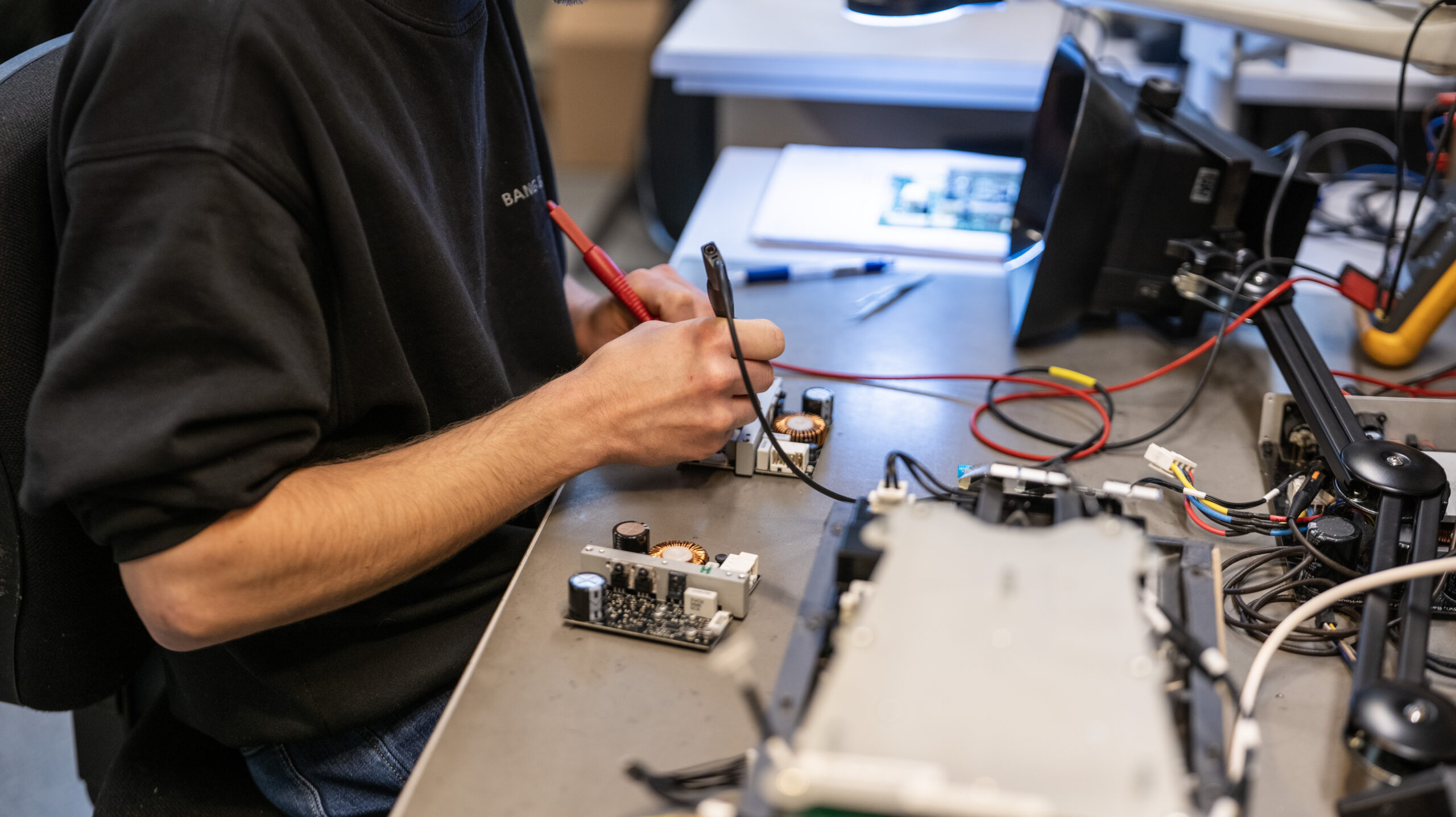
“We’ve had good success with the more expensive series, which are designed to be repairable,” says the guide, “but we haven’t got that far when it comes to repairing more affordable products like headphones and portable speakers. That will be our next goal.
And it makes sense that products that use glue instead of screws are harder to repair. It’s certainly possible, but perhaps not in as efficient a process as I see in Factory 3. Not yet, anyway. Still, it’s nice to see a manufacturer respecting their craft and moving away from the use-and-throw-away mentality that permeates much of the electronics industry.
When even TVs from the 80s and 90s are given new life here, I understand better why Bang & Olufsen still has such loyal fans. It’s about durability on all levels.
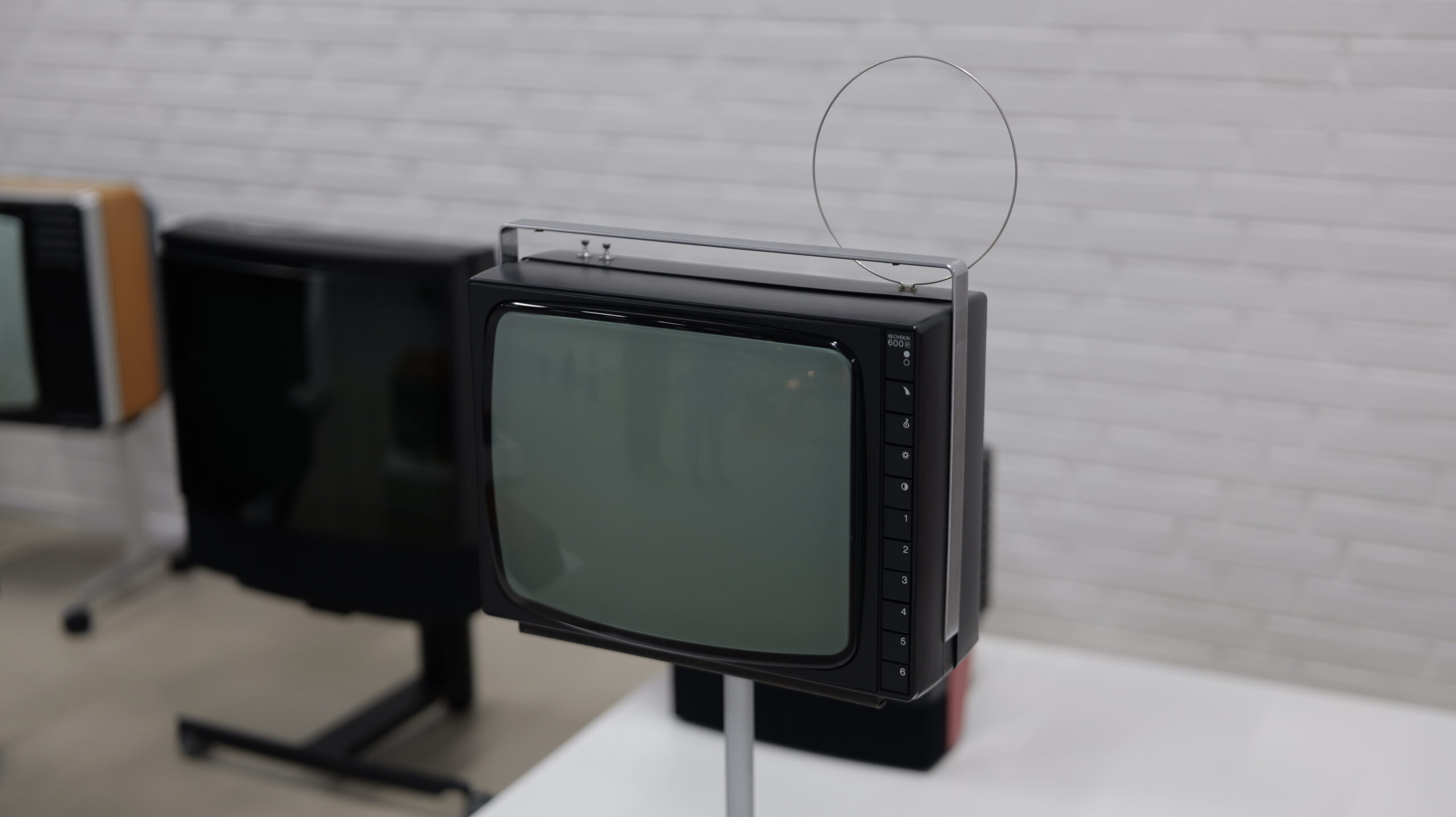
A test room with deafening silence
Finally, I get a listening session in the Bang & Olufsen test room, where “klangmeister” Geoff Martin welcomes me. In the soundproofed room, the silence is almost deafening. Acoustics expert Geoff explains that the room was built completely floating; a box-in-box construction that eliminated almost all outside noise.
As we sit in there, I eventually start to hear a faint hiss. Geoff explains that this is probably because the electronics are switched on, but it’s almost inaudible precisely because the room is so quiet.
“If you sit here alone for 15 minutes, you will start to hear the blood circulating inside your own head,” he says.
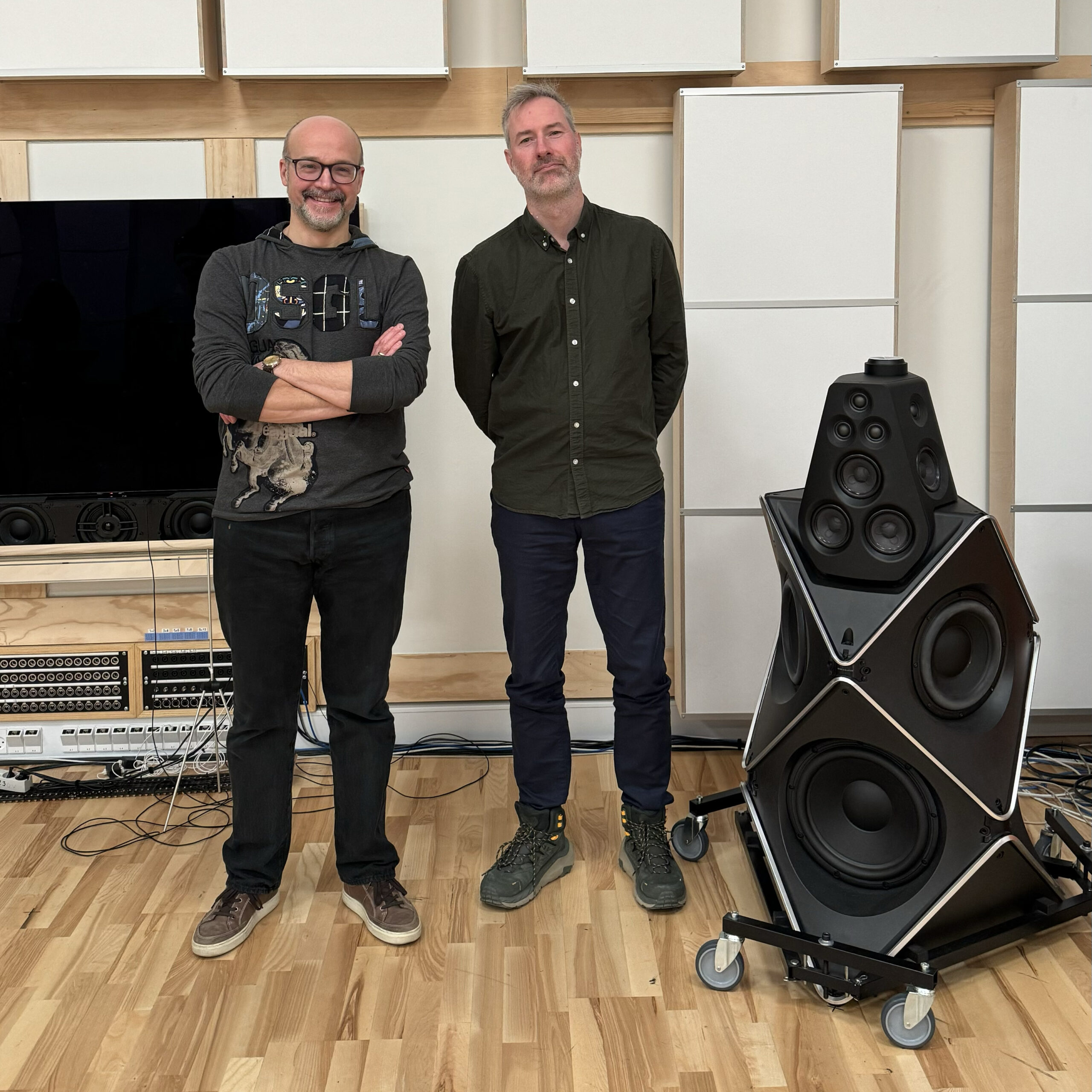
He adds that their measuring instruments are unable to detect how quiet the room actually is; they reach the noise limit of the measuring equipment long before the limit of the sound produced by the room itself.
I am impressed by how quiet and isolated the room is. Here, B&O’s engineers can test prototypes under ideal conditions, without any external interference. Geoff is enthusiastic and passionate about acoustics and sound, and with a pair of Beolab 90s, he really emphasises the uniqueness of this purpose-built test room.
The speakers are built with a special DSP technique that cancels reflections from the room before they reach the listener. I’ve never heard them as well as in this room, even though the difference with and without correction is greater in a normal living room.
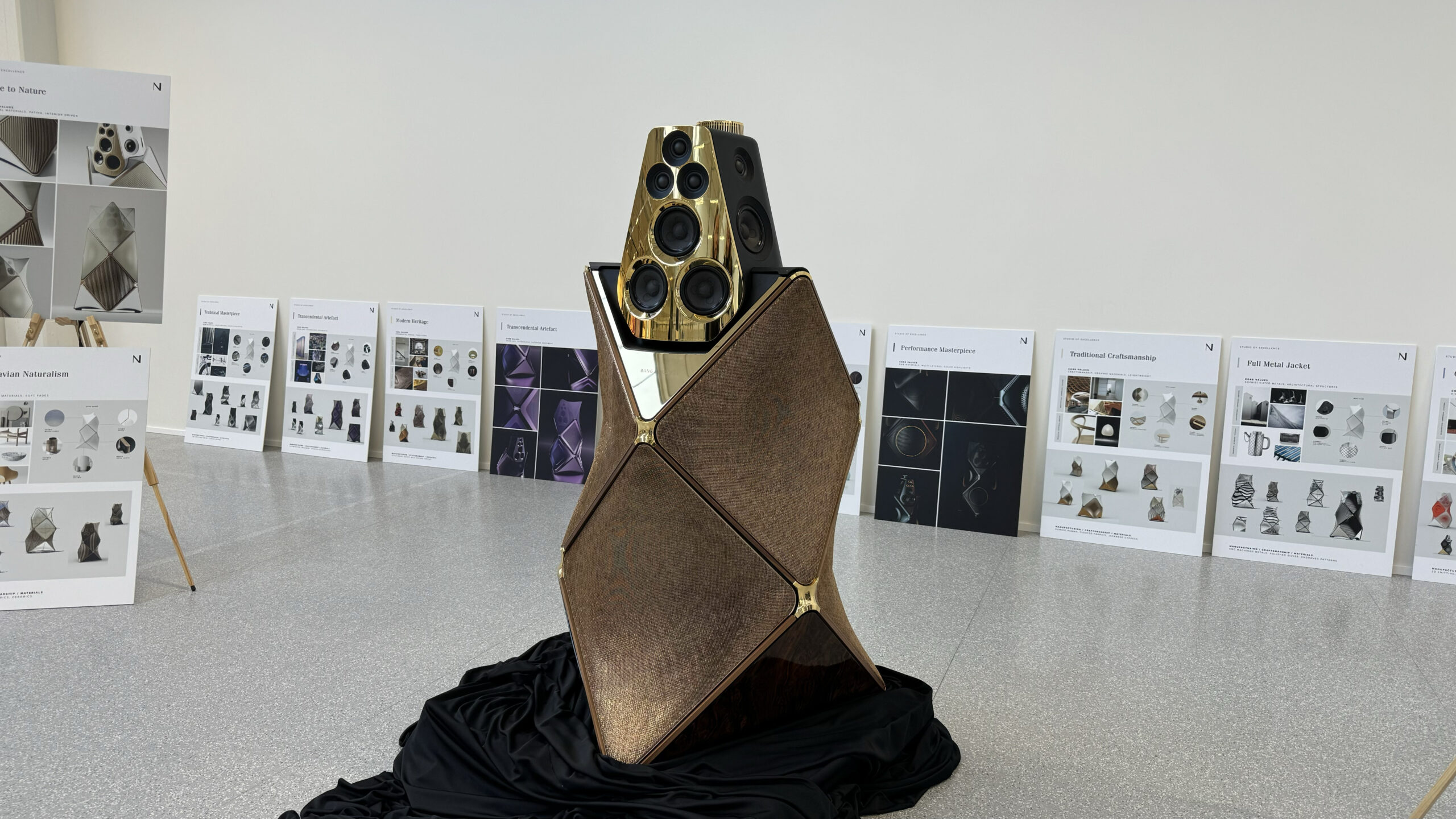
A proud heritage
The employees I speak to seem to really mean it when they say they have a love for the company and its products. This is also reflected in the Wall of Fame, which got a new image on the wall on the same day as my tour. I learn that many of the current employees have worked at the factory for more than 40 years, and some for more than 50 years. It’s quite incredible.
I leave Struer with a feeling of having seen something unique. A place where past and future merge, but where people are still crucial, even in an increasingly automated production.
B&O’s products are understandably perceived as luxuries. But with the passion, commitment and craftsmanship behind them, you realise you’re paying for something special.
More info: bang-olufsen.com
Excellent summary of an excellent company that produces special products indeed
I have been using there products half a century, still listening to B&O Bemaster 4500 and BL20. All the products are excellent craftsmanship and great design. My lifestyle is B&O.